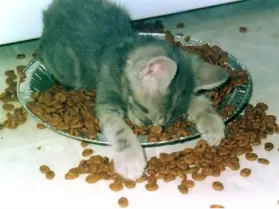
Is it possible to have too much of something? It seems kids never have enough toys; IT managers never have enough software, hardware or gadgets; Mechanics – tools; or pets - food. The list of seemingly insatiable objects is historical, and most, if not controlled, will get you in some kind of trouble. And so it is with inventories of aircraft parts.
Consider this: Worldwide the Jetliner fleet is comprised of about 17,200 aircraft. It is estimated that the global parts and components inventory to support that fleet is worth $44 billion. That’s $2.6 million per aircraft! Airlines hold about $1.6 million per aircraft with the balance held by OEM’s and suppliers. What this equates to is that “…airlines and operators have compiled around eight times the value of the inventory they actually need to support their fleets, simply because of difficult to resolve inefficiencies within the industry infracture.”1 While there are many issues contributing to those inefficiencies, a continually evolving and improving concept is of sharing pooled parts among different operators.
In the days of regulation, when code-sharing and airline alliances were just ideas, everyone was conceivably a competitor. The idea of sharing parts with a possible competitor did not sit well in many board rooms. Having large inventories of parts was ingrained as a way to be operationally independent, and to reduce delays and cancellations. In today’s financially challenged environment, great pressures are being exerted to reduce inventories, and so the parts pooling concept is growing in popularity.
As early as 1948, a few European airlines met and started sharing parts and resources. An organization was needed to facilitate the process. Today that organization is the International Airline Technical Pool (IATP). It now has 111 airline members that share 9,088 parts valued at over $265 Million.2 IATP, a nonprofit group, provides the structure, procedures, contacts, and administrative capability needed to make it work.
The parts pools are divided into 6 pools by letter groups:
- K: 707, 727, 737
- M: 747
- P: DC-9 and MD-80 series
- Q: All Airbus models, DC-10, MD-11
- S: 757, 767
- T: 777
If the concept works good for parts, what about other resources? The IATP also has pools of the following resources:
- Line Maintenance
- Maintenance up to and including ‘A’ checks
- Ground Handling Equipment and tools
- Access to 11 strategically placed Aircraft recovery kits (Kits that contain tools and equipment to help recover planes with collapsed landing gear, planes stuck in the mud or which have run off the runway/taxiway)
Here is a scenario that illustrates how the system would work for a typical airline. Suppose your airline is starting daily 777 service from your country to JFK. You would have to stock JFK with spares, trained line maintenance crews, tow bars, jacks, and ground support equipment. By joining IATP the airline can avoid having to make those capital investments at that location for just that one daily flight. The airline would pay a one-time entrance fee of $50,000, a membership fee of $1500 per season, and a $474 pool group (group T) fee per season. An example of the savings is the airline would have access to an Integrated Drive Generator for only $27,000 per year compared to the purchase price of an IDG at $450,000.
IATP itself does not perform any of the services; it just acts as a non-profit facilitator of the process. The services are performed by about 29 associate members of IATP who provide the parts, warehousing, maintenance, training, and ground handling. The majority of these associate members are not airlines, and all numbers cited change with some regularity.
Finally, the process to participate in IATP is not as easy as merely paying fees. In many countries the airline is required to gain approval from their Civil Aviation Authorities. These CAA’s are primarily concerned that the airline have published internal procedures to adequately control the process, and oh yes, the IATP will be in contact to judge the adequacy thereof, as well.
Overall, it’s a pretty neat system.
Gotta have more coffee, more coffee, more, more, more…
1 “Pooling Pays”, Aviation Week & Space Technology, page 38, October 12, 2009
2 “Pooling Together”, MRO Management, page 46, September 2009